It’s key for any business to focus on getting better. This helps make the workplace more efficient and encourages new ideas. By making things better, companies can make customers happier and do better overall.
It’s important to make improving a part of the company’s culture. This means using strategies and methods to bring about lasting changes. It’s also key to let all employees see and act on ways to get better.
Key Takeaways
- Identify and mitigate process improvements and safety hazards to save significant costs.
- Ensure company-wide support for Kaizen efforts.
- Help employees use continuous improvement strategies.
- Keep track of processes before and after changes for clear checks.
- Make work processes the same for ongoing betterment and more efficiency.
What is Continuous Improvement?
Continuous improvement means always trying to make things better in an organization. It started in lean manufacturing and now helps all parts of an organization work better together.
The word Kaizen comes from Japan and means ‘improvement’ or ‘change for the better’. It’s the base of continuous improvement. This method uses the PDCA cycle: Plan, Do, Check, Act.
- Plan: Look for ways to make business processes better.
- Do: Try out small changes.
- Check: See how things went and check against important goals like how fast tasks are done and how many mistakes there are.
- Act: Make the good changes bigger.
Improvement isn’t just about doing things faster. It’s also about making a place where people like coming to work. It’s key to listen to what employees say and check how happy people are with their jobs.
Keeping up with training and growth helps keep improvement going. But, teams might face problems like not wanting to change, not caring enough, or not having enough resources. To beat these issues, talk clearly, get employees involved, and make sure they have the help and tools they need.
According to McKinsey’s research, about 38% of companies using continuous improvement were trying to turn things around. The other 62% were using it to move from being successful to being the best.
Benefits of Continuous Improvement in the Workplace
Continuous improvement in the workplace brings many benefits. It makes products and services better. It also makes employees happier and customers more satisfied.
“70% of the most successful companies are always looking for ways to improve their operations and performance.”
One big plus is making the workplace safer. It means keeping work areas clean and safe. It also means fewer mistakes and a safer place for everyone.
It also makes work more exciting and motivating. When employees can share new ideas, they feel more satisfied. A study showed that happy employees make their companies do better.
It also helps meet customer needs better. This can make customers happier. Companies that improve often use their resources well and work better.
Finally, it helps companies stand out in the market. Look at Toyota and hospitals that use Six Sigma. They show how well these methods work.
The Plan-Do-Check-Act (PDCA) Cycle
The Plan-Do-Check-Act (PDCA) cycle is key in quality models and ongoing improvement. Walter Shewhart and W. Edwards Deming introduced it in the 1950s. It’s used across many industries for its effectiveness. This cycle, also known as the Deming wheel, supports kaizen, the Toyota system, and lean manufacturing.
Plan: Identifying Opportunities
The first step is to find chances to get better and plan how. This means doing deep analysis and planning to see what changes could work. The aim is to know exactly where to improve.
Do: Implementing Small-Scale Changes
Next, try out the changes on a small scale in the ‘Do’ phase. This is important to see if the changes will work. Testing small helps avoid big risks and gives useful insights.
Check: Reviewing Results
After trying out the changes, it’s time to check how they did. In the ‘Check’ phase, look at the results to see if they were good. Using data from this phase helps spot what worked or what needs more work.
Act: Scaling Successful Changes
If the changes worked, then scale them up in the ‘Act’ phase. Making these changes bigger can bring big improvements. The PDCA cycle keeps going back to planning to find more ways to get better.
Lean Methodology
Lean methodology started with Toyota in the 1950s. It aims to make processes better, cut waste, and always improve. This method focuses on using resources well and solving problems in a planned way. It helps make things faster and more flexible.
Eliminating Waste
Getting rid of waste is key in Lean, inspired by Toyota. It means cutting out things that don’t add value in making products. This helps companies focus on what customers want and work better.
Lean sees eight kinds of waste: mistakes, making too much, waiting, unused talent, moving things, having too much stock, extra movement, and doing things twice. Tools like Kanban and Work-in-Process (WIP) limits help teams see their work. They manage their tasks better and cut waste, saving money.
Boosting Efficiency and Morale
Lean makes things more efficient and lifts morale by pushing for constant betterment. It uses methods like SMED and value stream mapping to make work smoother and cut downtime. It respects people, making workers feel important and motivated.
With Kaizen, everyone helps find and fix problems. This leads to better teamwork and new ideas. Companies get more focused, work better, and their workers are happier.
Six Sigma
Six Sigma is a way to make things better using data and strict rules. It uses stats to make sure things work the same way every time. This helps make businesses better by cutting down on mistakes and saving money.
Quality Management Methods
Six Sigma is all about making things better with strong quality methods. It uses steps like DMAIC to find and fix problems. People in Six Sigma get different levels of training, like White, Green, and Black belts. Each level shows how much they know and what they can do.
Data-Driven Decision Making
Six Sigma relies on numbers and stats to make decisions. This way, it avoids guesswork and keeps improving. It uses tools like Process Flow Maps and Fishbone Diagrams to make things run better. The goal is to have almost no mistakes.
It also works well with other ways to get better, like LEAN. Together, they help businesses do better by making more money, working more efficiently, and making customers happier.
For more on how to keep making your business better, check out the Continuous Improvement Model.
Total Quality Management (TQM)
Total Quality Management (TQM) is a way to make things better and more reliable. It focuses on making processes better and cutting down on mistakes. It was started by Walter A. Shewhart and later improved by Joseph M. Juran and W. Edwards Deming.
TQM uses customer needs to keep getting better. This makes sure what we make is what people want and need.
Employee Involvement
TQM says it’s key to get employees involved. When employees help, they share great ideas that make things better and less prone to mistakes. They work harder because they care about doing well.
Customer Satisfaction Focus
TQM really cares about making customers happy. It makes sure what we offer is just what customers want. By listening to what customers say, we make sure our products or services are perfect for them.
This makes customers come back and helps us do things better by reducing mistakes and making things more consistent.
Kaizen Approach and Its Long-Term Impact
The Kaizen approach means “change for the better” in Japanese. It focuses on making small, steady changes. This leads to big improvements over time. It also makes sure employees are involved in making things better.
Small Incremental Changes
Kaizen is about making small changes that add up. Toyota started a system in May 1951 to get better ideas. These small changes helped make their products better and workers more productive.
The 5S method helps make work more efficient by getting rid of waste. Then, 6S adds safety rules to make work safer.
Building a Culture of Continuous Improvement
Creating a culture that loves change is key to Kaizen. Getting everyone involved is important. When employees share their ideas, it makes Kaizen work better and makes them happier.
Activities like Gemba Walks and Kaizen events help find and fix problems. They bring teams together to work on goals. Kaizen events are great for small teams, helping them improve quickly.
For a lasting culture of improvement, leaders must support it. They use tools like A3 and 8D reports to track progress. This way, everyone knows how changes help the company. Continuous improvement brings many benefits, like doing things better, saving money, and making quality better.
The Kaizen method’s focus on small, steady changes and employee involvement is key to success. It helps companies stay ahead in the long run.
Employee Engagement Strategies
Getting employees to feel connected is key to making work better and keeping up with changes. Sadly, about 80% of workers worldwide don’t feel engaged. It’s important to use strong strategies to make work places where everyone feels included and creative.
Regular meetings, surveys, training, time checks, and the Catchball strategy can really help. They make sure employees feel heard and part of big decisions. Since managers play a big role in how teams feel, it’s crucial they talk openly and clearly with everyone. This can make teams work 25% better.
When employees are engaged, it shows in big ways. They help make companies 23% more profitable, 18% more productive, and 10% better with customers. Celebrating what employees do helps build a strong company culture. This makes employees more likely to see promotions as fair and more likely to help each other out.
Helping employees feel good at work means offering flexible hours and good health benefits. These things make employees more committed and dynamic.
FAQ
What are continuous improvement strategies?
Continuous improvement strategies help make businesses better. They aim to improve processes, products, and services. The goal is to make operations better, make customers happier, and improve the whole company.
How does continuous improvement benefit workplace efficiency?
Continuous improvement makes work better by making processes smoother and cutting waste. This means work gets done faster and with less effort. It makes the workplace more productive.
What is the role of Lean methodology in continuous improvement?
Lean methodology is key in making things better. It focuses on cutting waste and adding value for customers. It comes from Toyota and aims to make processes better. It also makes workers happier and products better.
How does Six Sigma contribute to business performance enhancement?
Six Sigma uses quality management to cut down on mistakes. It makes processes very consistent. This leads to fewer errors, lower costs, and better performance.
What are the main components of the PDCA cycle?
The PDCA cycle has four main steps: Plan: Find chances for change and plan how to make it happen. Do: Try out small changes. Check: See if the changes worked. Act: Make the changes bigger if they worked, or try new ideas.
How does Total Quality Management (TQM) improve organizational processes?
TQM makes things better by focusing on quality and getting everyone involved. It aims for customer satisfaction and standardizes processes. This reduces mistakes and makes operations better.
What is the significance of the Kaizen approach in continuous improvement?
Kaizen is important because it focuses on small changes that add up. It encourages discipline and teamwork. This approach makes improving a part of everyday work.
How can companies enhance employee engagement in continuous improvement efforts?
Companies can get employees more involved by giving regular feedback and surveys. They can also offer training and use the Catchball strategy. This way, everyone can share ideas and help improve the company.
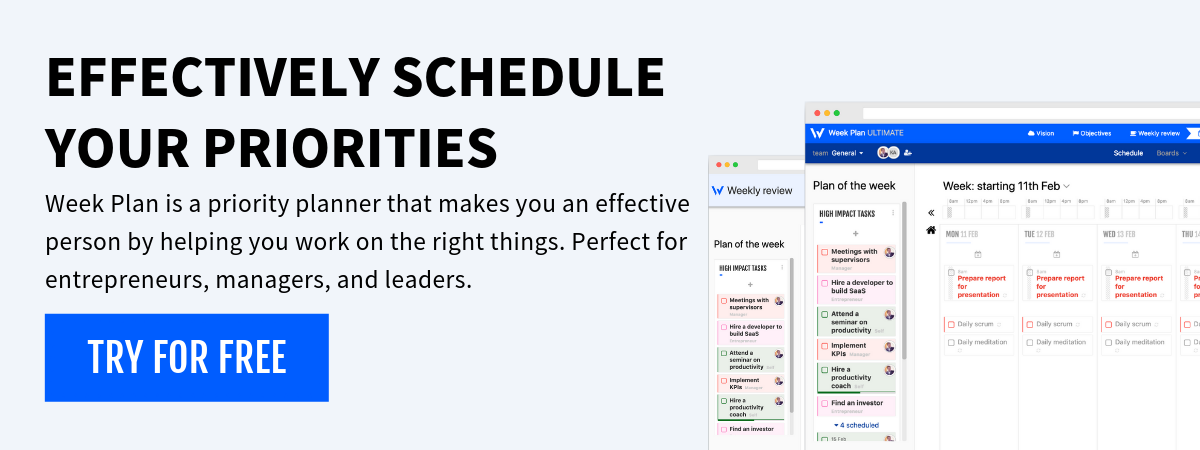
More Posts
What Kind Of Goals Will Set You Up For Success?
Week Plan Updates: Introduces Some More Great Features
What’s New in Week Plan 2.113.3?
Benefits of Personal Planner for Productivity & Organization
In today’s fast-paced world, maintaining productivity and organization has become more important than ever before. Whether you’re a student, a professional, or a stay-at-home parent, balancing multiple responsibilities and tasks can be quite...
Avoid Procrastination: 10 Lessons Learned from Daniel Walter
In today's fast world, distractions often stop us from reaching our goals. At work or in life, fighting against procrastination can lead to not meeting our goals. This can make us less productive...