Cycle Time Analysis stands as a critical evaluation method in both manufacturing and service industries, aimed at measuring the time required to complete a task or process from start to finish. This analytical approach focuses on identifying the actual time taken for activities, helping organizations to pinpoint inefficiencies, streamline operations, and improve overall productivity. By comprehending the concept of Cycle Time Analysis, businesses can make informed decisions to optimize their processes and reduce waste, leading to improved performance and customer satisfaction. Understanding cycle time as a valuable metric drives continuous improvement by identifying areas for enhancement and benchmarking performance.
Introduction to Cycle Time
Cycle time is a critical metric in various industries, including manufacturing, software development, and service industries. It refers to the time spent producing an item, encompassing all stages from start to finish, including any wait times. As a key performance indicator (KPI), cycle time enables companies to schedule accurately, order materials efficiently, and set realistic production and inventory budgets.
Understanding cycle time is essential for meeting customer demand and improving overall efficiency. By measuring cycle time, businesses can identify areas for improvement within their production process, streamline operations, and ultimately increase customer satisfaction. In the competitive landscape of today’s market, having a firm grasp on cycle time can provide a significant advantage, allowing companies to deliver products faster and more reliably.
The Basics of Cycle Time Analysis
At its core, Cycle Time Analysis involves tracking the time from when work on a task begins to its completion. Cycle time analysis is crucial for optimizing project management methodologies, as it helps in identifying bottlenecks and improving cycle times to enhance operational efficiency. It’s a straightforward yet powerful way to gauge the efficiency of production lines, workflows, or any processes that convert inputs into outputs.
Key Components of Cycle Time Analysis
- Start Time: When the process or task initiation occurs.
- End Time: The moment the process or task is completed.
- Cycle Time: The total elapsed time between the start and end times. Identifying both the start and end dates is crucial for effective project planning and understanding the project’s timeline.
Calculating Cycle Time
Calculating cycle time is a straightforward process that requires two key pieces of information: the total number of goods produced and the total time it took to produce them. The cycle time formula is:
Cycle Time = Total Time / Number of Units Produced
This formula can be applied to individual work items, batches, or entire production processes. For instance, if a factory produces 100 units in 200 hours, the cycle time would be 2 hours per unit.
To calculate cycle time accurately, businesses can use historical data, such as production records, to determine the average time spent producing one unit. By consistently tracking cycle time, companies can identify trends, optimize their production processes, and make data-driven decisions to improve efficiency and reduce waste. This ongoing analysis helps in pinpointing bottlenecks and areas where time can be saved, leading to a more streamlined and productive operation.
Cycle Time and Lead Time
Cycle time and lead time are two related but distinct metrics that are often used interchangeably in manufacturing, but they serve different purposes. Cycle time measures the time spent producing an item, including all stages of production and any wait times. In contrast, lead time measures the total time from when a customer order is placed to when it is delivered, encompassing production, order processing, labeling, and shipping.
Lead time is essentially the sum of cycle time and other operational processes. Understanding the difference between these two metrics is crucial for businesses aiming to improve their production processes. By focusing on both cycle time and lead time, companies can identify opportunities to reduce delays, streamline operations, and meet customer demand more effectively.
Optimizing cycle time and lead time not only enhances customer satisfaction by ensuring faster delivery but also provides a competitive edge in the market. Companies that can deliver products more quickly and reliably are better positioned to attract and retain customers, ultimately driving higher productivity and growth.
Importance of Cycle Time Analysis in Time Management
Understanding and managing cycle times is crucial for any organization striving to enhance efficiency and reduce operational costs. It provides valuable insights into the speed and effectiveness of production or service delivery processes, allowing managers to identify bottlenecks, unnecessary steps, or areas requiring improvement. By focusing on cycle time, organizations can foster a culture of continuous improvement efforts, unveiling inefficiencies and guiding teams to implement multiple improvements simultaneously and adjust strategies in real-time for better productivity.
Conducting Cycle Time Analysis: A Step-by-Step Approach
Define the Process: Clearly outline the process or task to be analyzed, including its start and end points.
Measure the Time: Use appropriate tools or software to accurately measure the time taken to complete the process.
Analyze the Data: Examine the collected data to identify patterns, variances, and areas where the process deviates from the expected norms.
Identify Improvement Opportunities: Pinpoint bottlenecks or inefficiencies that contribute to increased cycle times.
Implement Changes: Make the necessary adjustments to the process to eliminate waste and reduce the cycle time.
Repeat the Analysis: Regularly review the process to ensure continuous improvement and adaptation to changing conditions.
Examples of Cycle Time Analysis in Action
- Manufacturing: In a car assembly line, measuring the time taken from the start of the assembly process to the completion of a car helps identify delays or inefficiencies in specific sections.
- Service Industry: For a customer support team, analyzing the cycle time of resolving customer issues can highlight the need for additional training or resources.
Benefits of Cycle Time Analysis
1. Improved Efficiency
By identifying and eliminating process bottlenecks, organizations can reduce cycle time, achieving a smoother workflows and improved efficiency.
2. Cost Reduction
Streamlining operations leads to reduced production times and lower operational costs.
3. Enhanced Customer Satisfaction
Faster turnaround times result in higher customer satisfaction levels. From the customer’s perspective, understanding lead time is crucial as it involves recognizing their expectations for timely delivery and transparency.
4. Increased Productivity
The development team plays a crucial role in monitoring cycle time and enhancing efficiency, which allows for more tasks to be completed in less time, boosting overall productivity.
Challenges and Considerations
While Cycle Time Analysis is a valuable tool, it’s important to consider variability in tasks and external factors that may influence cycle times. Benchmark cycle times to compare operational performance against established targets and industry standards is crucial for understanding efficiency and identifying areas of overprocessing. Organizations should also ensure that efforts to reduce cycle times do not compromise the quality of the output.
Conclusion
Cycle Time Analysis is a vital component in the toolkit of organizations seeking to optimize their operations. By meticulously measuring and analyzing the time taken to complete processes or tasks, businesses can uncover inefficiencies, streamline their operations, and achieve significant improvements in productivity and customer satisfaction. Implementing cycle time analysis requires a commitment to continuous improvement and a willingness to adapt processes based on data-driven insights. Emphasizing process optimization through cycle time analysis can significantly improve efficiency and productivity, giving businesses a competitive edge.
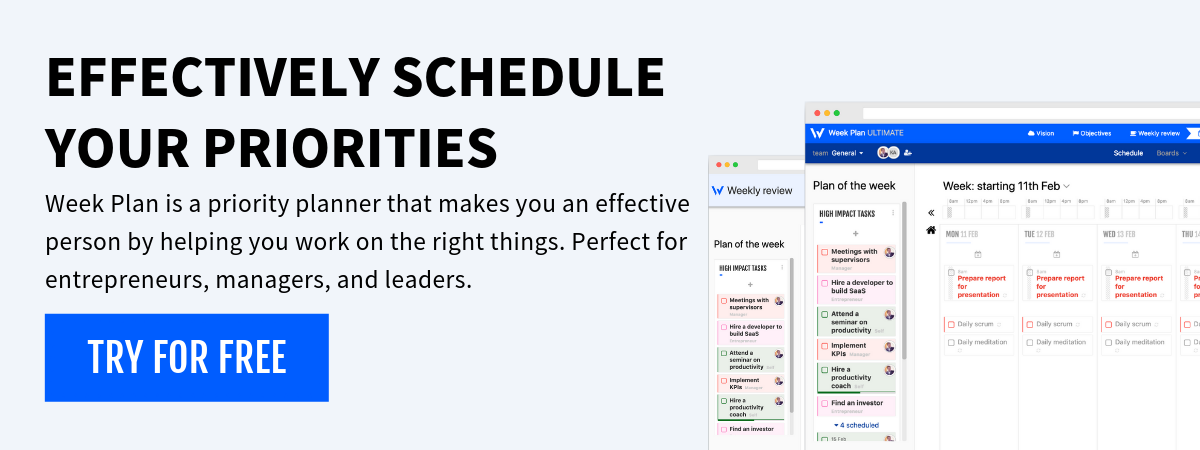
More Posts
The Future of Time Tracking: 13 Trends to Watch
The world of time tracking is constantly evolving, with new technologies and trends shaping the way we manage our workdays. With an increasing trend in remote work and on-the-go business operations, time tracking...
50 Top Task Management Software to Consider
Are you looking for task management software equipped with advanced features that can elevate the task management process, handling everything from individual tasks to complex projects? If the answer is yes, this article...
10 Ways How Anxiety Affects Productivity
Last year, many felt more stressed, depressed, and anxious, says the American Psychological Association. This rise in anxiety impacts how well people work. Amanda Augustine from TopResume notes that work anxiety often comes...
7 Best Monthly Goal Planners
As we navigate the busy streets of our lives, having the perfect tool to jot down, plan, and track our goals can be a lifesaver. Whether you’re into the classic pen-and-paper method or...